The 4 pillars of TVH’s Quality Management
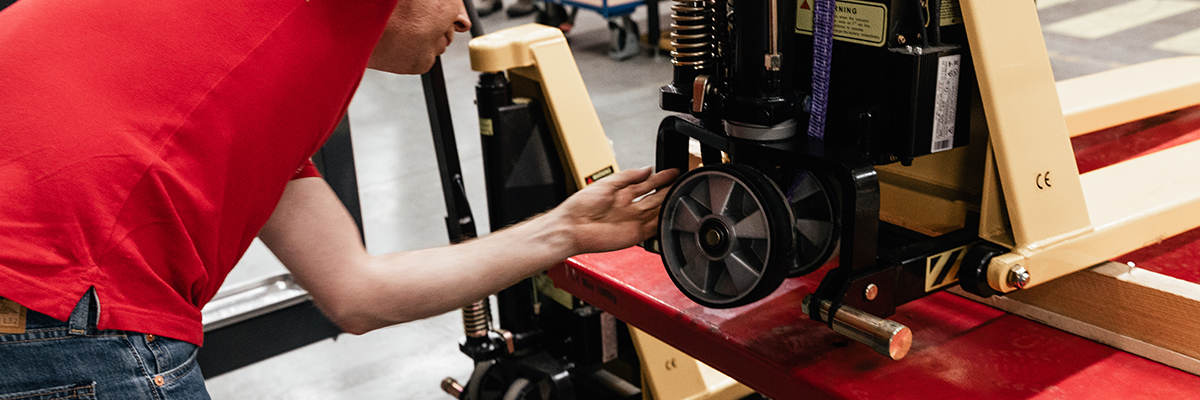
At TVH, we are committed to always providing the quality parts and accessories you need. To achieve our product quality commitment, TVH’s quality management is based on four pillars. TVH’s quality expert Björn Vansteenkiste talks about the importance of people, products, suppliers and processes.
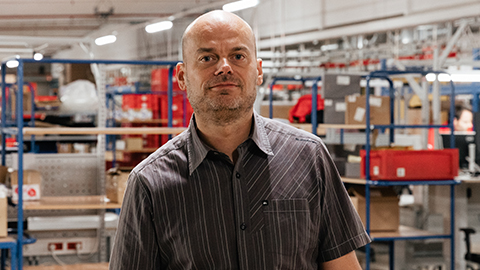
About the expert
Björn Vansteenkiste has been Quality Manager at TVH since 2020. He is responsible for the practical organisation of the quality teams to ensure optimum product quality control, but his commitment goes much further. He also plays an active role in promoting and integrating product quality assurance in all processes that affect product quality. Prior to joining TVH, he gained 22 years of experience in various quality-related positions in the automotive sector.
1. People
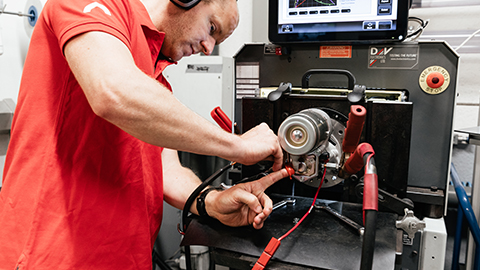
While the most obvious association regarding quality probably concerns products, this is not the first pillar. “We have a clear goal with TVH, which is to never compromise on quality. And the people in our organisation are key to achieving this,” Björn begins enthusiastically. “We have over 100 colleagues in our quality teams, who are dedicated to monitoring our products and ensuring that all parts and accessories are of the right quality.”
“However, it is important to note that TVH’s quality management goes beyond our quality teams. It requires the right mindset throughout the entire organisation. That is why we constantly create the awareness that quality is everyone’s responsibility.”
2. Product
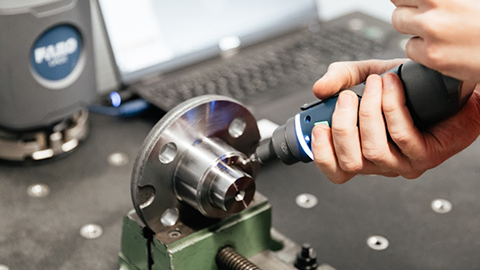
“In order to guarantee the quality of our products, the responsible people must of course be able to rely on predetermined quality requirements. Hence, specific standards have been set for our products,” Björn stresses. “A product is only applicable for inclusion in our range if it conforms to all safety and product regulations. In addition, its form, fit and function must be such that our customers experience a flawless assembly and performance that meets their expectations. These parameters are by the way not only used in product onboarding, but also in quality sampling at goods-in.”
3. Suppliers
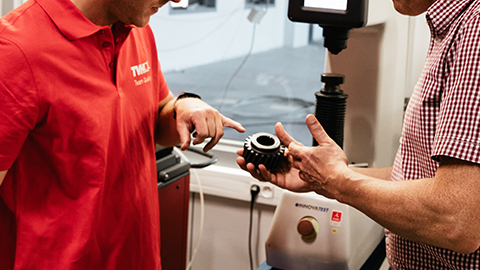
“Within TVH, we put a lot of effort into ensuring the quality of our products. But naturally, our partners also play a crucial role,” Björn points out. “We need to be sure that our suppliers can consistently deliver parts and accessories of the required quality. This is why we go through a selection process before starting to work with suppliers and why we always keep a close eye on supplier performance. If quality issues do arise over time, either through our own observations or through customer feedback, we also expect our suppliers to take appropriate action.”
4. Processes
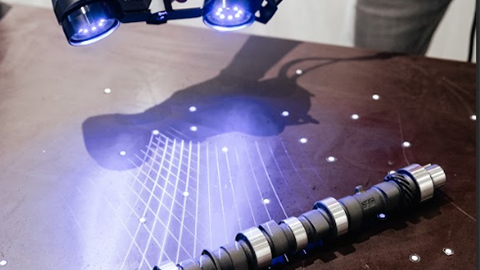
“To meet our quality commitment, we are constantly striving to improve product quality assurance in all processes that affect product quality,” Björn continues. “In addition, our quality teams have several quality control processes in place to ensure the right quality of all our products. First of all, there are several preventive measures so that flawed parts don’t get a chance to make it into our range. Therefore, both first article inspections before product onboarding and randomised inspections of incoming goods are standard practice.”
“But despite our best efforts, it is always possible that a problem will arise and that we will have to take corrective action. Imagine we receive a quality claim from a customer. This triggers a process to avoid similar quality issues in the future. The process starts with gathering as much information as possible to help us identify and analyse the root cause of the issue. Based on this analysis, we take appropriate corrective action, such as adjusting our global stock. The analysis also helps us to take the appropriate preventive actions. Sometimes this is as simple as updating the drawings. In more extreme cases, we may need to change suppliers. Finally, all preventive measures are validated, for example with new goods-in inspections and audits.”
“Measuring and testing products are at the heart of all our inspections, both preventive and corrective. We analyse the material, carry out dimensional checks, make 3D measurements, test the functioning of the parts on our various test benches … In short, we always do our utmost to ensure that our range is of the right quality!” Björn concludes.
Ready for more?
- Check out our brochures and catalogues to get an idea of our wide range.
- Browse and buy all parts and accessories in our online shop.
- Feel free to contact us if you have any other questions.
About the authors
This blog post is brought to you by your construction equipment marketing team.
Request your customer account to shop parts online
Submit the application form to specify your business needs and request your customer account.
Our sales team will contact you within 3 business days to talk about your business needs and complete registration.
After your account is set up, you will receive a personal login to our online shop. We will guide you in finding parts and placing your first order.
Request your account
Over 75.000 customers trust TVH as their spare parts supplier to ensure their client’s equipment fleet is running smoothly and efficiently. It starts with a customer account.