Quality in every part
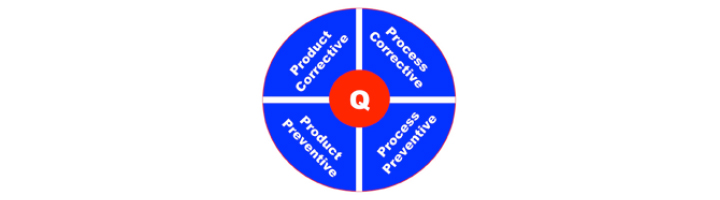
Quality is embedded in every step of our processes. Our four Quality Quadrants define our Quality Assurance policy, which is carried out by our team of more than 50 quality professionals every day. It outlines preventive and corrective improvements for both products and processes.
How do we assure quality products?
We want to create added value for our customers and suppliers by continuously improving our products and processes.
Supplier Rating & Sourcing
- Product quality: Matching OEM standards in terms of use, life cycle, dimensions and warranty
- Packaging: Suitable for transportation with minimal risk of damage
- Supplier reliability: On-time deliveries, response time, pricing and product availability
First Article Inspection
Before new suppliers are approved, our Quality Control Department thoroughly tests supplier samples. Over the years, TVH invested in advanced testing equipment, including hardness testers, spectrometers, 3D measurement tools, PCB testing stations, and more.
We test, compare and install samples on machines to evaluate their performance in real-world conditions. For hydraulic transmissions, our new universal testing bench ensures the highest quality. Customers receive a test report detailing the measured pressures at various RPMs, including cold and heated oil tests.
Incoming Inspection & Storage
We conduct random and systematic sample tests on incoming shipments, measure the parts and compare them with the product specifications. Those results are then fed back into our supplier rating system.
Approved parts receive a released-status, are individually packed, and stored under optimal conditions (humidity, temperature, etc.).
We are ready to offer the best service when things don't go as planned. If an issue arises, we work with your trusted sales advisor to find the best solution. Interested in how we handle quality claims? Watch our video now.